Today, manufacturing companies are continuously looking for ways to reduce operating costs while eliminating contamination risks and minimizing environmental footprints.
A critical manufacturing tool used for a variety of applications is an air compressor. Choosing the right kind of air compressor to suit your company’s needs can help you to achieve your goals in the long run.
One of the most significant decisions you need to make when choosing is whether you want a lubricated air compressor or an oil-free air compressor.
Switching to an oil-free system can help you to better meet the minimum requirements for air quality regulations in your industry. These requirements vary by industrial application, with the most stringent standards applying to those manufacturers whose end products, packaging, or critical instrumentation come in direct contact with compressed air.
What is the difference between lubricated and oil-free air compressors, and which is right for you and your business?
What is an Oil-Lubricated Air Compressor?
All air compressors operate basically in the same way. A steel or aluminum piston or rotary screw element is used to draw air in from the surrounding area. This air is then compressed and stored in a reinforced tank until it is needed.
Related: Rotary Screw vs Piston Air Compressors
In order for the piston or rotary element to move smoothly and consistently, it needs to be lubricated with oil. This can cause an additional challenge because then the oil mist will need to be caught before it can enter the manufacturing plant, damage equipment, and contaminate your products.
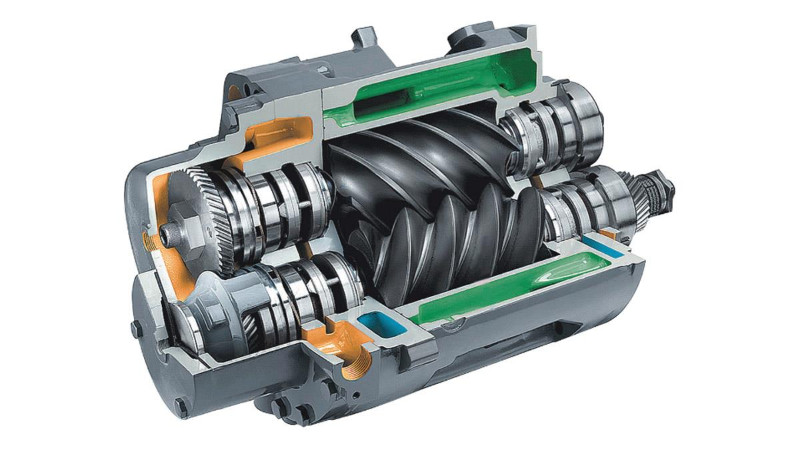
What is an Oil-Free Air Compressor?
Although an oil-free air compressor also uses a piston or rotary element, oil is not needed for lubrication. This is because the compression element is coated with a pre-lubricating material such as Teflon. This creates a low friction environment with no need for oil.
Teflon’s use in high friction applications, such as air compressor cylinders, has become increasingly popular in recent years.
Some oil-free compressors also may use water instead of oil as lubrication. Not only do these alternative materials solve the problem of having to clean up oil spray, but they can also protect the pump.
Related: Benefits of On-Site Nitrogen Generators
The use of naturally lubricating solids enhances the safety and reliability of the manufacturing process. The mechanism will still move smoothly and without the need for any oil-based or synthetic lubrication.
Oil-Free vs Oil-Lubricated Air Compressor?
The main difference between the two is that one uses oil and one doesn’t, but you should be aware of a few other significant differences.
Oil-lubricated air compressors will require more routine preventive maintenance, with oil needing to be changed every so often, whereas there is nothing to change with an oil-free compressor.
The excess oil of the oil-lubricated compressor will need to be removed in order to protect equipment and processes from contamination. This will require the need for more air filtration like separators and coalescing filters.
It is also important to consider that energy consumption can account for up to 90% percent of an air compressor’s total life cycle cost.
By switching to an oil-free compressor, coupled with a variable speed drive, new control system, and a heat compression dryer, you can cut energy costs while providing clean, dry, oil-free air for food plants, pharmaceutical production, and a variety of other applications.
Benefits of an Oil-Free Air Compressor
Worry-Free Operation
Oil-laden compressed air can cause damage to air treatment systems and process equipment. This can then affect sensitive electronic components and cause unnecessary expense and too much downtime in your manufacturing plant.
Related: Air Compressed Systems Maintenance Tips During Summer
Risk-Free Legal Compliance
Some manufacturing processes cannot risk contamination. Some industries require a very high purity of clean, dry, oil-free air. With an oil-free compressor, you get peace of mind, both in your system and for your business.
Lower Maintenance Costs and Energy Savings
A true oil-free air compressor does not have any oil at all in the compression chamber. Consequently, this will minimize downstream filtration requirements and pressure drops, which will directly translate into energy savings for your company. An oil-free system operates with less maintenance and higher reliability than an oil-based system.
Increased Sustainability
With the high-quality, contaminant-free air that you will get from an oil-free compressor, you can be sure that you are helping make your compressed air system as streamlined and efficient as possible.
Conclusion
With lower maintenance and operating costs and superior air quality, oil-free air compressors are becoming an increasingly popular option for many industries requiring high air purity, such as pharmaceuticals, food processing, electronics, and many others.